Or, the story of how my poor wife gets her lounge back.
Like most small businesses, HappyMoose had a humble beginning. We used to store our single printer and all the supplies in one study. When I needed to work, I'd walk in and closed the door behind me. Not bad.
As the business grows, we added more machines, more shelves and more inventories. Before Zephyr, my wonderfully supportive wife realised, the operation has taken over the lounge. Yup, the family lounge, including our only fireplace and the only heat pump too. (Don't judge me, please. I have been a good boy otherwise, eating my veggies, brushing my teeth and putting out the garbage on time. Well, most of the times.)
Last December, we heard that there was a near-new digital press coming to the market with a considerable discount. I knew that this machine would allow us to produce many new products, cards, books, much cheaper and faster. I also knew that to take the business to the next level, we need a production grade machine like this one.
With a massive smile and a definitely-non-trivial monthly payment plan, I signed the contract. Little did I know just how much efforts we need to find a home for this beast.
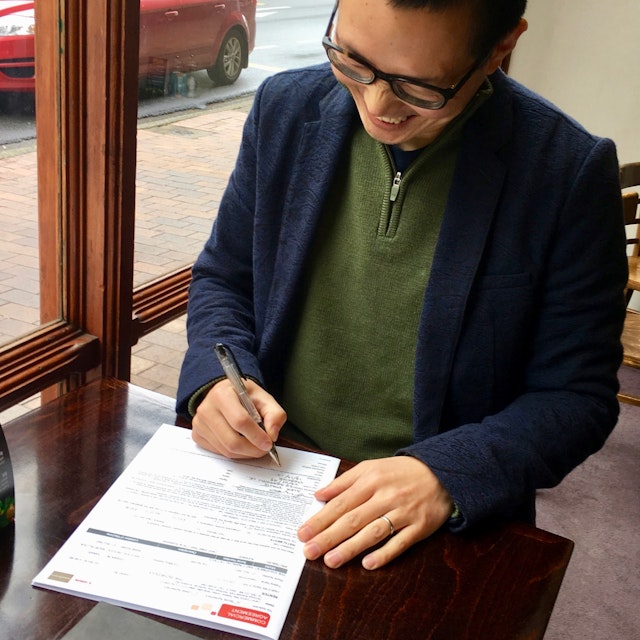
We set the machine's delivery date to be March. Three months away; there's plenty of time left. I remember telling myself.
Fast forward to the end of February. I realised that we had a significant challenge in front of us.
It turned out that the machine weighs more than a ton, too heavy for most building floors. And it's so power hungry that it requires a dedicated meter, a full set of 35amp circuit breakers and high-grade wiring. Most office spaces offer a handful of 10amp power sockets. This puppy needs at least two 15amps and ten more 10amps ones.
Making things even more complicated is our limited budget. Because we're running this business mainly from cash flow and family saving, budgeting out $5k for the electricity rewiring is already pushing us into overdraft. Not to mention all the bills we have to pay and the slow sales we would have for the first a few months after installation.
I kept ringing up Canon to push off the delivery date. February turned into March. March became April. The picture looked bleaker as the days went by.
By early April, we had exhausted almost all options. There seem to be only three possibilities left on the table. All equally unpalatable. We could rent a dungeon-like underground storage space and try to insulate it, add lighting and re-wire it up to spec. We could also rent an old fish-n-chip shop that's behind a one-dollar shop, which at least meets the electrical requirement but the smell was ... not great. Or, please do not laugh out too loudly, we could convert our master bedroom into a print room.
April 12th was a Thursday. It was raining and cold and miserable.
I was in my study going through my contact list one last time to see who I haven't called that might know the commercial rental market. As luck would have it, I found out that Nigel Bamford, a successful fellow entrepreneur, had just bought an old foundry building a couple of weeks ago. I rang him up right away. By 5:00 I was already standing inside the building.
The building was not exactly fancy, but it ticked all the boxes. Nigel and I shook our hands that evening, and by Friday lunchtime, I had the keys in my pocket.
Things moved a lot faster from that point on.
We had an industrial electrician who works for Nigel coming in to install the fittings and power sockets. Following his suggestion, we replaced the old fluorescent lights with 4 LED light bays. They are not only cheaper to run, but also, crucial for us, offer the best viewing light condition for photography prints.
The graphic arts and printing industry have recognized the need for uniform, consistent and technically accurate print viewing stations for years. Traditionally, print houses would pay a lot for Print Viewing Stations. What these devices offer are D50 (5000K – the industry standard) light sources in an enclosure suitable for viewing prints and judging their colour balance. It just happens that these LED bays already run at 5000k. Lucky. Yeah, I know.
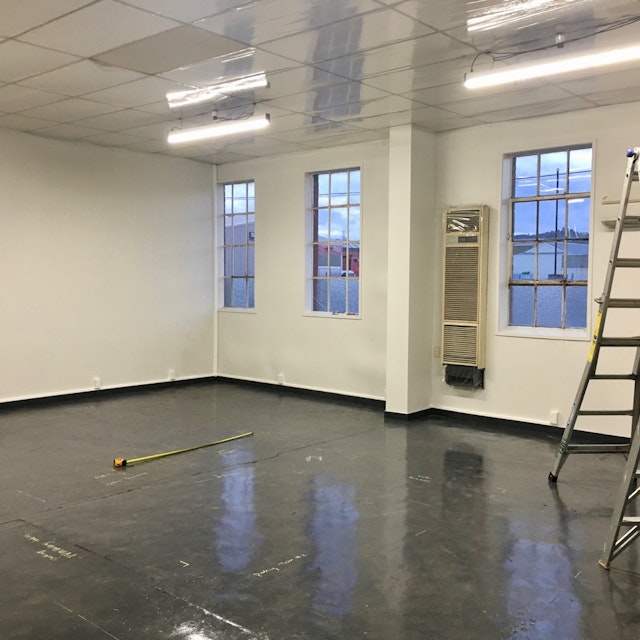
One major downside of getting a space in an old foundry is that there is fine dust everywhere, which the Canon site surveyor pointed out as soon as he stepped into the building.
All the printing equipment require a dust-free environment. An industrial grade clean-room setup would easily bankrupt us ten times over. Nigel came up with the idea of using painter's film to seal up the ceiling tiles. We put the film up before a few windy days set in, and it seems to hold up well.
The picture below shows the two of us putting the film over the last tile. It was a great upper body work-out, but my neck and shoulder didn't seem to share this optimistic feeling.

It has been a great honour to work so closely with Nigel and see him solving issues on the fly. In a 2017 paper on Entrepreneur's Personality Traits in Harvard Business Review, the authors argued: "researchers have primarily gravitated to the Big-5 factor personality model, including self-efficacy, innovativeness." This statement pretty much summarised how a successful entrepreneur like Nigel operates. He does not throw money at problems. Instead, he looked at the issues he had, then experimented carefully with different materials, ending up getting the same result much cheaper and faster.
May 22nd was the delivery day.
The foundry has a massive sliding door that's five meters high. Unfortunately, the truck was about 20cm too tall to squeeze through. So we had to move the printer into the room by pushing it across a rough concrete floor that's more than 200 meters long. The printer is high precision equipment, and the bumpy surface would almost certainly damage the circuit boards inside.
The driver, whose full-time job is to deliver massive yet fragile equipment throughout South Island, had three cast-iron sheets that are just wide enough for the printer to roll on. So the four of us built a track for the printer. Kind of like how the tractor's track works. The photo below shows Carl moving the last board to the front so the printer can keep inching ahead.

In the tech industry, there is always a discussion of the self-driving trucks would replace human drivers. I am not sure whether these pundits understand the jobs that are involved as being a professional driver. Our little move-in exercise has shown that the value of a human driver is way more than knowing how to get from place A to place B. A lot of his experience lies in dealing with the unknowns once the truck has arrived at the destination.
Here is a photo showing the machine assembled. Our large format printer, using inkjet technology, operates perfectly fine under a wide range of conditions. But the new digital press uses laser and hot plate. It needs to work at a constant temperature and humidity. So the workshop has a heat pump that's going 24x7 to make sure that the printer is happy, content and ideally purr once in a while.
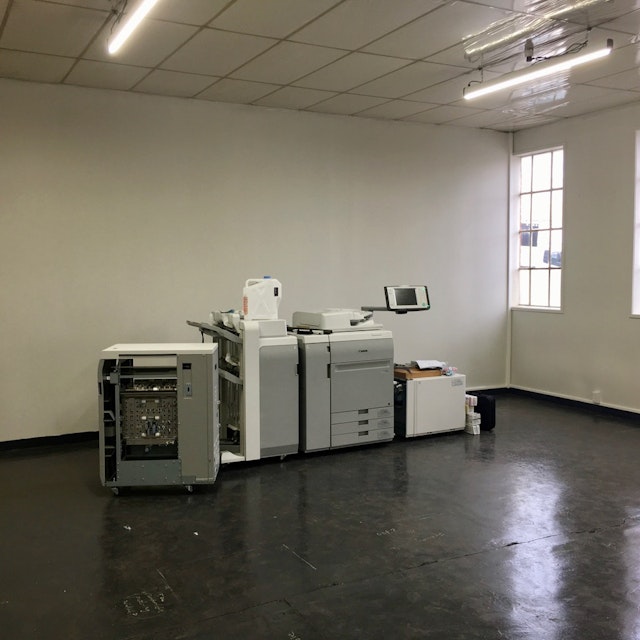
Here is a photo of the workshop shortly after we get everything set up correctly. We have customers asking about those pink nappy boxes. We use them extensively in our studio. Together with MDF panels, they are perfect in adjusting the height of the work surface, so we don't need to bend down all the time.

The fibre worked on 2nd of June;
We moved all the shelves, inventories and machinery from our lounge to the new workshop on the 3rd.
The new product "moments" went into public beta on the 5th,
And our first production run happened on the 6th.
So that's it. A new chapter in HappyMoose's life.
If you live in Dunedin and you'd like to meet the team behind this service, come and say hi to us at 2 Tewsley Street!